Cutting through the Surface: Methods for Processing Compact Surfacing By Chad Nichols & Jeff Evans
TIMES ARE CHANGING. And if you are a fabricator of hard surfaces, you’ve likely noticed the changes coming for a while now. You have also probably had some time to decide how you feel about it, and, if you’re like some, you may not like it. But not liking it won’t change your customers’ demand for ultracompact materials. So the better question is, what are you going to do about it?
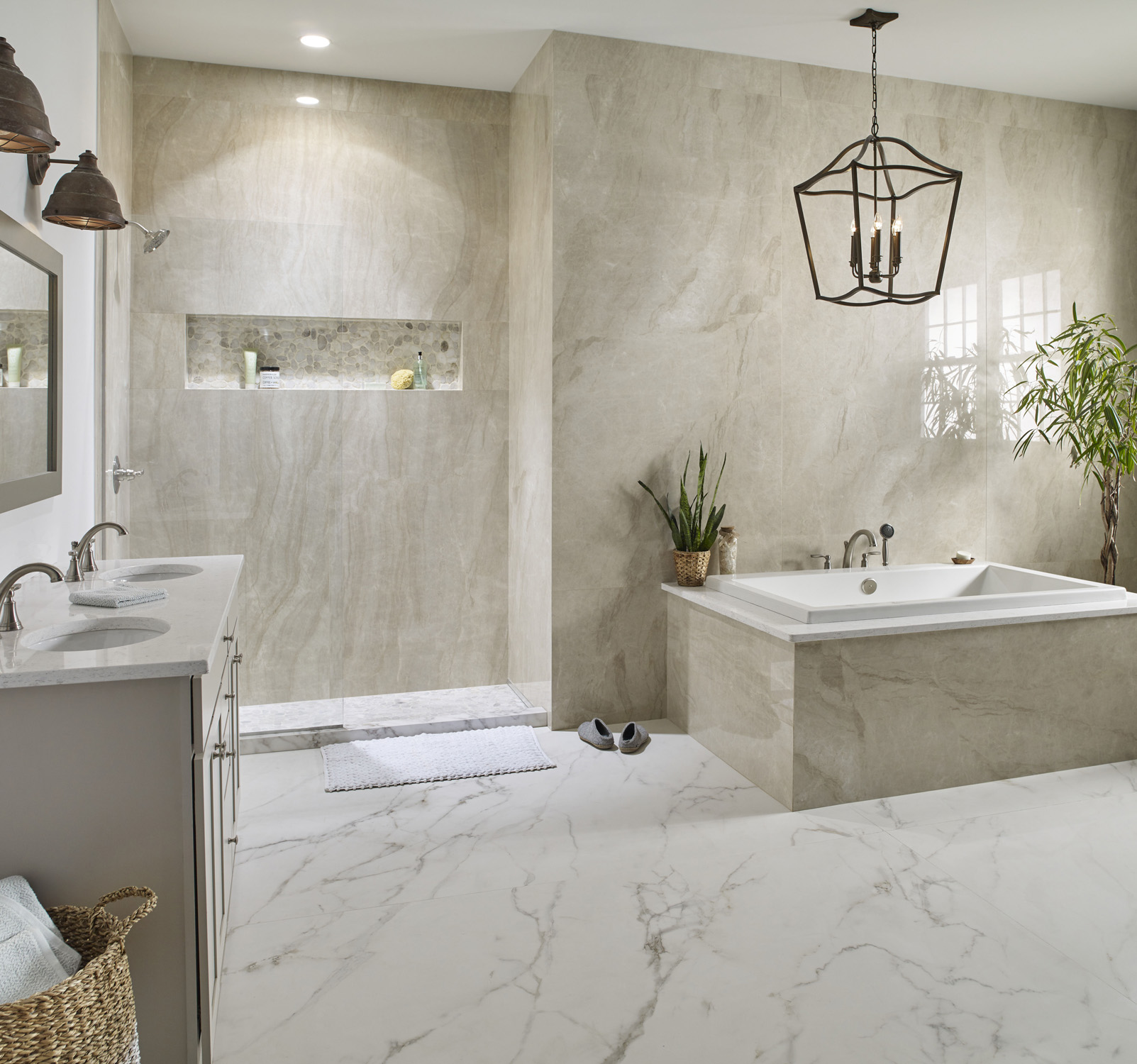
Ultra-compact materials are not new. Porcelain, in particular, has been around, particularly in Europe, for some time, and, while relatively new in the United States, it has been gaining popularity as a countertop and cladding material. Similar to the transition from natural stone to quartz, the demand for porcelain is growing. If you don’t embrace the coming change and modify your business to be able to fabricate this material, there is a strong possibility you will miss market opportunities and your business will lag. Conversely, to embrace the notion that porcelain is here to stay could mean a huge upside for your business as its popularly grows.
So what do you need to know?
Material Characteristics
Porcelain is typically thinner than most other slabs, whether natural stone or quartz surfacing. Generally, you’re going to be working with material that is only 6mm, 12mm and 2cm versus a more standard 2cm or 3cm thicknesses common in natural stone and quartz slabs. This is important for a few reasons.
First, porcelain edge profiles are typically mitered. The material is not intended to apply an edge profile other than a miter edge because the color generally is not consistent with the surface through the entire material (not yet, anyway). A side-view of the cut edge will typically show a white cross section below the printed pattern. Because of this, as well as to improve the overall appearance of the installed porcelain, fabricators will generally be creating a mitered edge with a drop apron for thickness and consistency of grain.
Second, the material is light and more brittle than many fabricators are used to, and so it will require great care when cutting. To avoid damaging slabs and cut parts, the saw/sawjet feed rate should be varied. The blade may glaze if the material is cut too slow or too fast and that creates the risk of chipping, cracking or breaking the slab. With porcelain, cut quality is critical in producing an exceptional finished product.
Lastly, safety must be kept in mind. When handling porcelain, fabricators have to be cognizant of how sharp the cut edges can be. Porcelain can cut a person as easily as glass, so proper personal protective equipment is a must. Safety glasses, steel toe boots, hearing protection and cut-proof gloves should be worn at all times when handling and sawing porcelain.
Cutting Porcelain
There is a variety of strategies that can be employed to fabricate porcelain. Worth noting, more horsepower won’t help you in any of them. Fabricators are not going to be powering through a slab of porcelain because it will cause a considerable amount of rework and waste because of chipping and breakage.
In all cases, a good strategy is to start slower, ramp to a higher cut rate and then slow again as the equipment exits the cut. Cutting as slow as 15 inches per minute (IPM) as when entering and exiting the cut will improve the quality and help avoid breakage. Additionally, varying feed rates in this way will help keep the blade from glazing. A variable frequency drive (VFD) also helps, allowing you to adjust the RPM of the blade while you cut. Some machines are equipped with pre-programmed cut sequences designed specifically for ultra-compact materials that will automatically adjust parameters on the machine while it cuts.
Porcelain and blade manufacturers will have recommendations on arbor speeds based on the size of the blade that is being used. For example, with a 14-in. blade, an arbor speed of 1,900 to 2,500 RPMs and a feed rate of 30 to 100 IPM works well for straight cuts, whereas an arbor speed of 1,900 RPM and a feed rate of 25 IPM is more suitable for miter cuts. These recommendations are very close to the many manufacturers’ recommendations, although just a bit slower, which tends to yield higher quality cuts. This also assumes the use of a VFD. If using a machine that doesn’t have a VFD, a fabricator will be locked into an arbor speed (typically 1,700 to 1,750 RPMs), and may have to play with the feed rates, or try different blade sizes to get the same quality of cut. In either case, it is important to remember that cutting too fast or too slowly will cause the blade to glaze. When becoming accustomed to cutting with porcelain, it is critical to pay close attention to what RPM and feed rate works best for a particular setup and machine configuration. Remember, shorter cuts require slower speeds — fabricators may not be able to increase to the speed they’d like before having to start slowing for the exit cut.
Also worth noting, unless otherwise indicated by the slab manufacturer, porcelain does not have tension bands like other ultra-compact materials. There should not be a need for cutting to relieve stress, nor should blade pinching be a problem.
Finally, any time material is being cut, it’s smart to listen to the blade. More seasoned fabricators already do this, likely without thinking about it, and will hear what’s happening in the cut. If blade starts to glaze, it will definitely be apparent by the sound the blade is making.
Blade vs Waterjet
Both traditional saws and waterjet equipment perform well in cutting porcelain, much as they do with natural stone and quartz, and both have specific applications for which they are best suited. With blade cutting, operators can plunge wherever they’d like, and the porcelain on either side of cut will still be usable. A good feed rate for plunging is 5 to 7 IPM. However, it is key to be aware that plunging with the blade for several consecutive cuts will increase the risk that the blade will glaze.
The best plan when using a waterjet is to pierce an inch or so from the good material to avoid popping. For those who haven’t experienced popping, it’s when a small, circular chip gets knocked out of the surface of a slab. Obviously that is not something anyone wants happening to their parts. Having some room when first piercing, particularly when adjusting to cutting porcelain, is a good thing. Once an operator becomes more proficient, the distance needed for the pierce will be able to be reduced. As far as pressure, 20,000 PSI is a good pressure for piercing, and cutting at 25 IPM will provide a quality cut for both straight and miters. However, the waterjet can cut as fast as 100 IPM, adjusting for the quality of edge that is desired.
A sawjet combines a CNC saw and a waterjet, and is a great solution in cutting porcelain. Generally speaking, a ratio of 85 percent to 15 percent blade to jet works well to ensure quality cuts while balancing the cost of consumables.
Once again, it cannot be stressed enough when cutting porcelain, the feed rate is critical regardless of whether a blade, a waterjet or a sawjet is being used. Machine capabilities and the application will dictate which one will work best.
Tools and Table Support
Another important consideration is tooling. Continuous rim blades were initially thought to be the preferred blade for cutting porcelain, but we’ve actually found that segmented blades seem to perform better. The gaps in the blades allow more water into the teeth of the blades, and reduce the likelihood that the blades will overheat and glaze. Several blades performed well, and we encourage fabricators to experiment with which ones work best with their machine settings and configuration.
The importance of ample water on the blade can’t be overstated. Not only is it important to have an adequate water supply, but also good hose placement that covers the whole blade as it cuts is key. A blade will get hot as it cuts porcelain, and lots of water, hose placement, and a segmented blade are good strategies to keep your blade cool.
With regard to the table, there are several options for support. In all cases, it is important to make sure the table is perfectly level. Working with thinner, more fragile materials does not afford the rigidity of thicker materials. For tables that have rubber slats, making sure they are in good condition is essential. Tables with cement board should be checked to make sure the sheet is fresh and similarly in good condition. For poured concrete tables, using a 1- to 1½- in. rigid foam board on top of them will help reduce vibration and the likelihood that parts will move. Keep in mind that adding cement or foam board may add to the hight of a table, meaning adjusting machine parameters will also be required.
Order of Cuts
Working with thinner materials poses a challenge in the order of cuts as well, but this can easily be remedied. As the material is cut, it may shift — porcelain is very light. Therefore, a good practice is to make miter cuts first, straight cuts second and finish with the jet. It is best to cut the smaller pieces first, then finish cutting the larger pieces. This will help maintain the stability of cut parts as the process moves forward. Another good approach is to “onion cut” slabs, cutting from the outside in. In all cases, it is a good idea to try to keep the pieces connected as long as possible, which will reduce the chances that they will move, chip or break. Most importantly, as pieces begin to become free from one another, go slowly. Cutting too fast will increase the likelihood that pieces shift, thereby increasing the chances of costly breakage.
Embrace Change
Your overall opinion of porcelain may vary, but there’s no ignoring that it’s here and here to stay. It’s also safe to say that it will likely gain in popularity among designers, so your only decision now is how (and when) you will react to this growing trend. It seems logical that embracing the inevitable sooner rather than later could be a solid plan. Remember, when you’re first starting out, take it slow. As you gain experience with the material, your confidence and ability will likewise increase, and then you can ramp up. The discomfort of learning will pass, and you will be well on your way to a successful future with porcelain.
About the Authors
Chad Nichols and Jeff Evans are experts on stoneworking equipment with Park Industries, North America’s largest stoneworking equipment manufacturer. Nichols is the Executive Coordinator at Park, and has been in the industry for more than 15 years. Evans is a Product Manager and worked as a trainer and installer prior to moving to his current role. For more information about the company, contact Park Industries at (800) 328-2309 or visit www. parkindustries.com.
|